Case of India
Summary
For the full paper: LCD06-Vashist and project details |
Authors: Ms. Dandapani Varsha & Ms. Kriti Nagrath, Development Alternatives
Background
The construction sector accounts for 8.2% of India’s GDP and, as the second largest employer, employs an increasingly large workforce ranging from labourers to contractors and architects. Besides social and economic implications, the construction sector has
critical environmental implications.
- The sector contributes to 24% of greenhouse gas (GHG) emissions, 80% of which is borne by building materials (Parikh, Panda, Ganesh-Kumar, & Singh, 2009).
- The brick sector alone generates 42 million tonnes of CO2 annually, and uses 20–30 million tonnes of coal and 350 million tonnes of top soil (DA, 2012).
- The construction sector consumes 30% of national electricity, with an annual growth rate of 8% (Girija, 2011).
- Production technologies have additional implications, such as black carbon from brick kilns that further contributes to warming. Growth in the construction sector will be further fuelled by addressing the current housing shortage of 18.78 million (MHUPA, 2012) and meeting future demand of 44–48 million by 2022 (KPMG, 2014). Adding to this is the likely need for reconstruction in the wake of numerous disasters. Considering that in India 70% of the building stock required by 2030 is yet to be constructed (NRDC & ASCI, 2012), the potential impacts of the construction sector are rather grave. However, pathways to sustainability do exist. Cleaner technologies could substantially reduce the ecological footprint of the sector.
- The use of fly ash and vertical shaft brick kilns considerably increase resource efficiency in the brick sector.
- Cement production can be made less resource-intensive, thanks to the vertical roller mill technology, fluidised bed cement fired kiln systems and the use of fly ash in Pozzolona Portland Cement (PPC).
- Alternative building materials can reduce resource consumption by 25-30% (DA & CDKN, 2013).
- With proven commercially viable technologies, energy consumption in new and existing buildings can be cut by an estimated 30-80% with potential net profit during the building’s lifespan (UNEP SBCI, 2007).
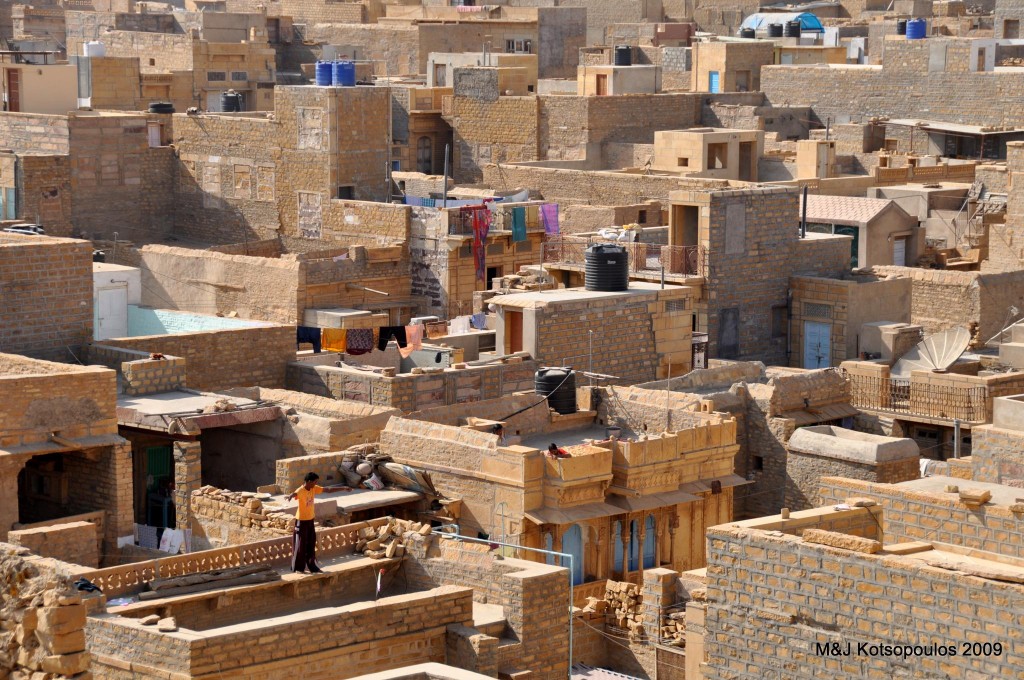
Measures to Accelerate Adoption of Low-carbon Technologies
There are options to increase the use of low-carbon, energy-efficient and disaster resilient construction alternatives in India at national and local levels as discussed below.
Policy and Regulatory Norms
India’s commitment to promote alternative and low-carbon technologies in the construction sector can be visualised through several policies and initiatives. The National Housing Policy advocates the use of alternative technologies and a holistic approach to sustainability. Both the 12th Five Year Plan (2013-2017) and the National Action Plan on Climate Change have identified green buildings and construction as a focus area. However, the translation of the mandate to policies and schemes has been minimal. To remedy this, guidelines should be developed to include the aspects of green construction in policies and schemes. This includes inclusion of low-carbon building materials in the Schedule of Rates, standards and specifications of low-carbon building materials, eco-labelling systems to ensure adherence to these standards and mandatory procurement guidelines for the government. It is also crucial to allow flexibility in the design and applicability of these materials subject to local climate and cultural demands.
Technology and Capacity
Currently, the Indian construction sector suffers from a lack of appropriate technologies and support in efficient technology transfer. Innovation of low-carbon and resource-efficient technologies is essential for the transformation of this sector. Several aspects need to be addressed for the successful adoption of these technologies. Technologies that include collaborative research, technology demonstrations, access to information and capacity building of workforce. The lack of technical capacity is one of the largest barriers facing the sector. Policies should focus on addressing this by organising technical training of masons and engineers on a regular basis. Capacity building of officials for the proper implementation of these policies should be promoted (TARA, 2014).
Market and Finance
The disaggregated nature of this sector throws up challenges with respect to strengthening the supply chain of materials and services. Continuous supply of construction materials can be ensured by setting up micro enterprises. Fiscal incentives and priority financing for Small and Medium Enterprises (SMEs) should also be initiated to facilitate setting up green building material production facilities. Quality is a key component in the aggregation of green construction services. Standardised curriculum and a system for certified skills for masons and artisans will go a long way in monitoring and assuring quality. Common interest groups and guilds can be leveraged to strengthen this cadre of skilled personnel.
Partnerships
It is vital to promote public-private partnerships (PPP). In such partnerships, the services are delivered by the private sector, while the responsibility of providing service rests with the government. PPP would not only help in commercialisation of low-carbon technologies, it would also aid stricter implementation of these policies. User acceptance of these technologies is the key to its acceptance. Limited information about the benefits of these technologies, its viability in the local context, and the operation processes hinder its growth. Awareness generation that targets users needed.
RecommendationsNational level
Local level
|
Case of Nepal
Summary
For the full paper: LCD06-Vashist and project details |
Constraints for Mainstream Alternative Construction Materials in NepalWith increasing urbanisation, the number of traditional buildings has decreased dramatically in the past six decades. They were gradually replaced by modern buildings made of contemporary building materials such as brick, cement, concrete, steel and aluminium. Traditional mud-and-stone houses were common in the past and designed to suit the local climate using traditional knowledge. The materials used, such as soil, stone, timber, bamboo and wood, were mostly available locally. The National Housing Policy 2012 mentions that 57% of the houses in Nepal are constructed with cement mortar, 27% with mud and stone and the remaining 8% with wood, bamboo and other temporary materials. There are existing practices of using low-carbon construction technologies such as hollow concrete brick (HCB), compressed stabilised earth block (CSEB), bamboo housing, earth rammed housing and traditional mud stone houses, which are comparably Due to an imbalance between supply and demand, there is limited availability of LCCM in the market. There is also a lack of readily accessible and reliable information that compares alternative structural materials and systems. Further, there is a lack of quality assurance for LCCM available in the market. No norms or guidelines exist for manufacturing these alternative materials, and monitoring mechanisms are lacking to ensure the quality and strength of these alternative, sustainable materials. This poses barriers in public acceptance. (SBCI, 2007). |
Case of Pakistan
Recommendations
For the full paper: LCD06-Vashist and project details |
Background
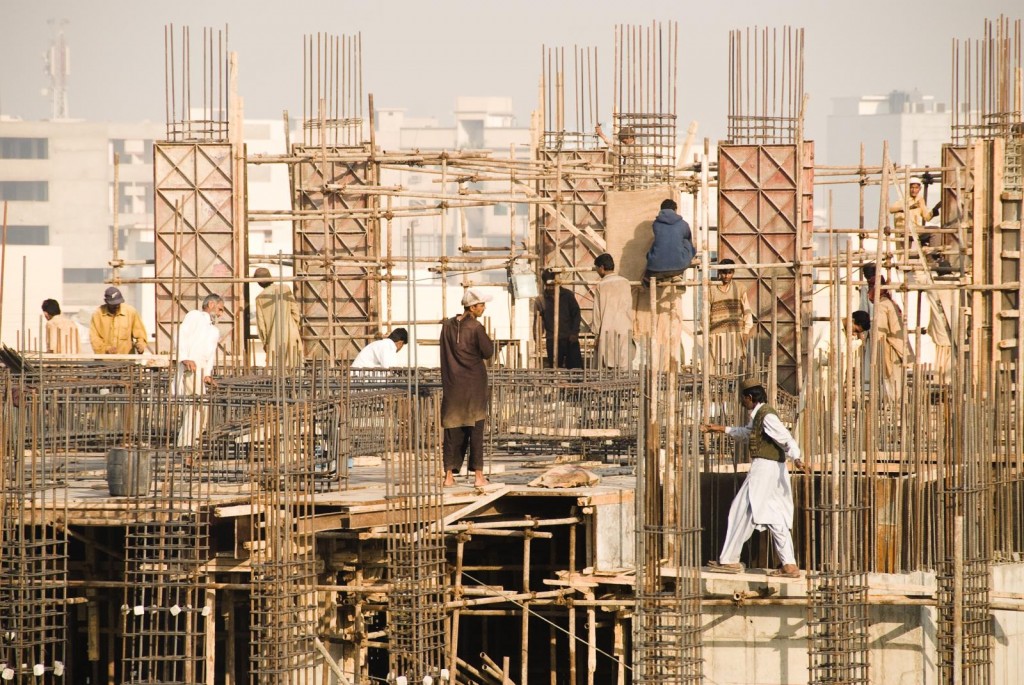
Authors: Ms. Hina Lotia & Ms. Sundus Siddiqi, LEAD Pakistan
The construction sector in Pakistan is consistently growing. With an average growth rate of 1.2% during 2000–2004, it experienced a great boom during 2004–2007 when it grew at an average rate of 18% per annum (Neilsen, 2010). Expansion in the construction sector is a result of the progress in socio-economic indicators of the country, as well as reconstruction efforts in the wake of numerous disasters. Floods alone have led to the collapse of over two million homes since 2010. Disaster-resilient and low-carbon reconstruction has been given very little consideration in Pakistan as disaster response is unplanned, urgent and makeshift.
Raw materials used in construction are infamous for utilising inefficient technologies that consume large amounts of coal and release high carbon emissions. The production of every tonne of cement results in an emission of at least one tonne of carbon dioxide (CO2); the production of every tonne of steel releases over two tonnes of CO2 into the atmosphere (Mahzuz, Ahmed, Ashrafuzzaman, Karim, & Ahmed, 2011). Due to these environmental hazards, the status of public health and the quality of urban life are degrading day by day in Pakistan.
Policy Implications
|
Research Findings
Three case studies in the construction and infrastructure sectors were evaluated for this brief. In the first, the Department For International Development (DFID) and HANDS used lime as a stabilising agent to reconstruct damaged or destroyed houses in the most affordable, resilient and energy efficient manner, thus synergising disaster risk management and low-carbon construction. However, there was lack of widespread acceptance and implementation due to lack of awareness, absence of research, dearth of good quality limestone, social taboos and lack of government bodies and institutions backing the cause.
The second case study explored VSBK as an energy efficient technology used for fired clay brick production. After runningVSBK kilns running on full capacity for a year in their project called Energy Efficient Brick Production (EEBP), the Swiss Resource Center and Consultancies for Development (SKAT) and Swiss Agency for Development and Cooperation (SDC) found that:
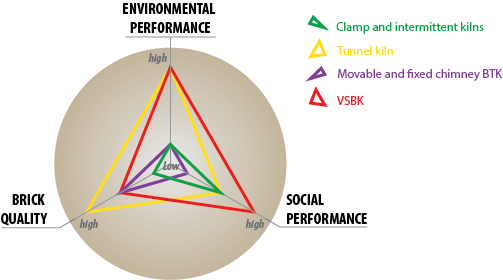
- High quality VSBKs can be established with local material supply, within the expected price level.
- VSBK bricks can compete with the upper brick quality segment of the Pakistani brick market.
- A correctly operated VSBK reduces energy consumption (and CO2 emissions) by 30–50%.
- First production cost assessments have confirmed that a full scale VSBK will generate considerably higher profits than a traditional brick kiln and that its comparative advantage will further increase with the rising coal price. (SKAT EEBP, 2010)
- VSBKs considerably improve working conditions, in particular by reducing exposure to toxic gases and heat, and will offer alternatives to bonded- and child-labour exploitation.
The kiln industry in Pakistan, as in other Asian/South Asian countries is conservative in nature. Most of the investors and technical personnel are not trained at any institution and are more concerned about a quick return on investment, thereby depending upon traditionally available technical knowhow and manpower. New and innovative technology is negatively perceived. While introducing the VSBK concept, these factors play an extremely important role in the lack of acceptability and ownership of the technology. The third case study illustrated the architectural, structural, environmental and technical performance of bamboo as a low-carbon and disaster resilient alternative to conventionally used material such as steel, cement and brick. The study looked at work done by the Heritage Foundation – an organisation pioneering the work on bamboo construction in Pakistan via their Green Karavan Ghar initiative. This technique of construction was tried out when the 2010 floods struck Pakistan. The first project undertaken was in Swat where 300 Green Karavan Ghar were constructed in remote mountainous areas from October 2010 to February 2011. Also, over 100 Green Karavan Ghar were built in a perennially flooded area in Khairpur. The Heritage Foundation also constructed floating bamboo structures on stilts as women centres, schools and health facilities. These structures endured the 2011 floods, providing refuge to the community on the upper level while the waters flowed through the stilts — proving that such green structures are not only environmentally friendly, but disaster resilient as well.
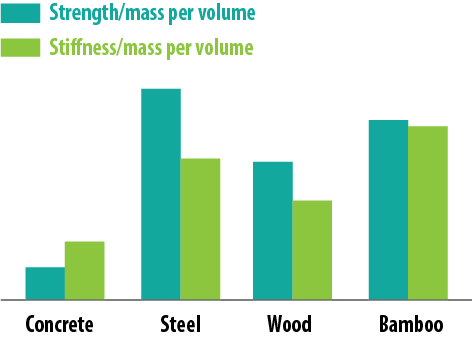
With the use of mud and bamboo, people are able to construct their own houses and produce the material that is used, incurring little or no labour cost considerably bringing down the cost of construction. Also, such low-carbon construction employing indigenous material actively involves the people and ensures that women are able to continue to contribute in home-making. Other than the ownership and pride that this system flourishes, it also trains the community and makes them aware of the different ways various materials are employed in construction, and teaches them the best methods for achieving low-carbon, green construction. This is probably the most long term benefit that comes out of such an endeavour — the education of the people with regard to low-cost, low-carbon construction.
This policy brief is developed for APN project “Identification of Policy and Institutional Gaps, Drivers and Strategies to Scale-up Low Carbon and Energy Efficient Technology Application in the Construction and Infrastructure Sectors in South Asia” (LCI2012-01NMY(R)- Vashist; LCI2013-01CMY(R)-Vashist) under APN’s Low Carbon Initiatives Framework. For full details of this project, including technical reports and other outputs, please visit the project metadata page. |